Working with Porcelain and White Stoneware at High Fire Temperatures
I’m a potter who works on the wheel, primarily making pots for the kitchen table. I have many expectations of the fired white stoneware and porcelain high fire clay bodies I create and use. A few of them are:
To achieve the clarity of glaze color I desire, I use porcelain bodies which fire to a white background. Then transparent or translucent glazes can gain maximum clearness as reflected against the white background of fired porcelain or white stoneware.
Creating a “Just Right” Feel
As a potter who works on the wheel, I need maximum workability from the clay I use, a kind of springy resilience and ability to stand up on the wheel. In the making of stoneware, iron-bearing fire clays and ball clays are used to excellent effect to create a kind of dense, “just right” feel.
In a porcelain body where only kaolin (china clays) are used, this excellent throwing quality is difficult or impossible to achieve, even with the addition of wet-mixed plasticizers. Kaolin (china) clays are also silica-poor, requiring up to 30% or more added (non-plastic) silica to achieve proper glaze fit, further reducing the workability of the porcelain.
This is why I enjoy creating white stoneware high fire clay bodies – to incorporate light-burning ball clays into the body to allow me increased ability to make larger forms while still attaining relatively white fired color.
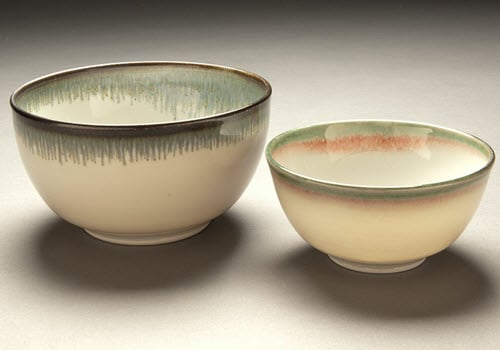
Eliminating a Potter’s Enemy
If a potter hopes to make sound, durable pots in high-fire ceramics, the formation of cristobalite (a primary phase of silica) is a deadly enemy. Cristobalite must be eliminated in the body by the use of a sufficient quantity of feldspar added to the blend of clays. This lowers both the absorption of the fired body (near 0% for porcelain) and the CTE (the coefficient of thermal expansion and contraction). Cristobalite is then absorbed into the melt at between 1280 – 1300C, high-fire temperatures.
Higher shrinkage rates are part of the deal with porcelain in comparison to stoneware clay bodies, especially stoneware bodies that contain percentages of grog or sand. A stoneware potter might expect 10 – 12% shrinkage in his fired wares, but a porcelain potter might encounter 17 – 20% shrinkage of their fired porcelain.
Thinking Bigger
Oversizing of thrown porcelain pots in the making phase must be anticipated. Imagine your amazement after packing a tight kiln and opening the door to a finished and cooled firing – and witness a whole lot of space where little existed previously.
Porcelain and white stoneware high fire clay bodies must also be engineered to keep warping at a bare minimum. Cracking of the body is eliminated in the process of combining feldspar, silica and plasticizer into the blend of chosen kaolin (china) clays.
Perhaps the most important reason I make my own porcelain and white stoneware is to ensure that my fired clay will fit a wide variety of glazes.